Why Is Fabric Inspection Machine So Important?
- LT Labs
- Aug 26, 2022
- 3 min read
In the context of the apparel business, the phrase "inspection" refers to the visual examination or evaluation of raw materials, partially produced garment components, or final garments. In addition, it evaluates finished garments by evaluating them against established standards, criteria, or specifications to ascertain if they are up to par or not. When deciding on whether or not to acquire an item of clothing, the quality of the fabric is always taken into account. Today's garment wholesalers, retailers, and customers all have high expectations for product quality and uniformity with established norms. Fabric damage may result in a discount of 45–65%.
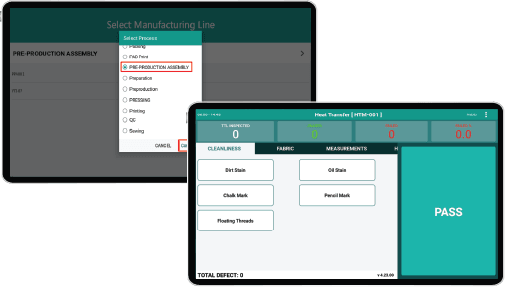
Given this, fabric inspection is a crucial part of making clothes. Inspection, which verifies the fabric's quality, is typically done before the production process for the garment ever begins. Inspection's major purpose is to detect nonconformities and defects as early as possible in production. The goal is to reduce the time and energy spent repairing the problem or getting rid of defective clothing down the line.
Types of fabric analysis grading systems
Fabric inspection refers to the visual examination or evaluation of partially manufactured raw materials. Fabric inspection is the procedure of visually inspecting raw materials, semi-finished garment components, and final garments to ensure they conform to established quality control measures and customer demands. The inspection of fabrics also includes the taking of garment measurements to guarantee compliance with standards. At least 20% of the total number of fabric rolls must be inspected for the quality check to be considered successful.
When purchasing fabric by the roll, the finished garment's quality is determined solely by the quality of the cloth itself. If inferior materials are used in production, not even cutting-edge technology can save the product. Twenty percent of the rolls they get are reviewed using multiple criteria. Any issues with the fabric's quality can be ironed out using this method before production begins.
All thriving textile businesses share a common goal: developing marketable fabrics. Competitiveness gains are very sensitive to improvements in textile manufacturing's output rate and quality. There has been a growth in the number of losses sustained by the textile sector as a direct result of subpar textiles. In the least developed nations, human inspection is still used to find most manufacturing flaws in textiles. Inspectors put in long hours of labour that are physically demanding. They have to spot tiny details that might be anywhere in a huge, rapidly-shifting region of their visual field. Probably somewhere around 70% of people can correctly identify you. Furthermore, once fatigue sets in, visual judgments lose their precision dramatically. In the recent decade, the evaluation of textured materials has become more reliant on methods from the field of digital image processing.
The precise and early-stage detection of flaws in the textiles is a key component of quality improvement as it allows for the reduction of waste in manufacturing.
Outline the possible discrepancies between human visual inspection and computerized inspection.
As a result of defects, the retail price of textile fabric might be marked down by as much as 65%.
There has been a lot of research in recent years into the ability to recognize patterns in the visual field that are unconstrained by factors like position, size, brightness, and orientation. Automated inspection systems using machine vision to detect flaws in textiles have been the subject of study for quite some time. Despite this, there is still a dearth of research in machine vision, and it was only recently that an automated system employing a neural network pattern recognizer was developed for identifying problems with textiles. A three-tiered, multilayer perceptron network with full connectivity was used for object recognition.
Comments